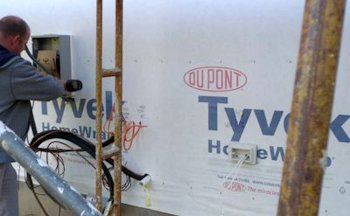 |
|
Believe it or not, Tyvek is required and even inspected in Montgomery County.
Sounds kind of monopolistic to me.
|
Here, the electrical panel is mounted on a one inch spacer. You'll see why below.
I don't trust Tyvek anyway so we put on a layer of felt paper before we put on self-furring
metal lath.
|
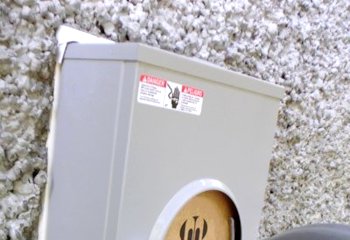 |
|
Fast forward to the finished wall shows how
we capped the spacer and the electrical box
with metal flashing. This prevents any rot
behind the panel.
|
Porch was done in 2003 leaving a gap between
the bottom of the stucco and the porch.
This looks a lot neater than a sloppy gob
on the bottom.
Also the gap provides relief from building movement, drainage for the stucco, and
the ability to replace the boards in the future.
|
|
|
On the 2014 porch we put flashing on the ledger board.
A piece of the finish floor material and a piece
of masonite were used to gauge the plaster
stop.
The new flooring will slide easily under the stop.
|
Porch roof from 2003 shows the gap between
the stucco and the flashing was never caulked.
These gaps should never be caulked !
The gap is a water exit for the stucco.
|
|
|
The windows and even the soffits are covered with plastic and tape.
Pebble dash splatters all
over the place and the mission is zero clean up.
|
A view of my office.
Mortar boxes are raised off the ground to
minimize bending and stooping.
Bags are stacked high to minimize lifting.
|